JAMIE PETERSON'S GUIDE TO FIXING GM
"Insanity" is defined as repeatedly doing the same thing over and over again; all the while expecting a different result. After 40 years of decline, you think someone at GM might have noticed that all is not well at home. It's time to try something new, because what you are doing is failing miserably.
BEAN COUNTERS
Common practice dictates when adopting any program, idea, or project from the upper echelon, that you make it look good by charging the expense to other projects. Often the project is worthless and it lingers around for a while before being scrapped and never yielding any profit.
Accountants cannot allocate resources efficiently if they have no clue as to where the money is going. Every money account must be set on strict accounting standards with severe penalties for misallocation of funds or reporting errors. However there should be no penalty for going over or under a budget, and any deviation must be reviewed to identify the root cause.
WASTE REDUCTION
Train people to squeeze out the waste in manufacturing and train them to train others. Billions of dollars are wasted each year simply because workers do not have the proper training. They learn enough skills to keep things inching along and huge sums of money are wasted as a result.
UNEMPLOYMENT WAGES
GM must shed the costly practice of pay for no work. Each laid-off employee should be entitled to one month's pay for each year worked. However lay-off pay should also be limited to one year, after which the employee would be terminated.
COMMUNICATION
Everyone has some great ideas to improve the workplace or corporation. Many of the ideas are creative and worthy of merit. Yet, it is rare to find anyone who would work to implement a better practice. The good-old-boy system and the God/Garbage Syndrome (people above you are infallible Gods, those below you are garbage) worked to stifle any creative input from the bottom up. The loss to GM has been unfathomable. Poor morale and cynicism have darkened the halls at GM for decades thus hindering any real progress. A plan must be developed to foster the free flow of information and creativity from the bottom all the way to the top.
A merit or bonus pay system for constructive ideas should be implemented through an impartial arbitrator or ombudsman that would report directly to the President of the company.
LEADERSHIP
The ability to lead is a regressive movement in America. There are very few natural born leaders at GM. The rest at least were content in their ability to get things done and keep the organization functioning normally. There were very few really bad leaders and those of wisdom usually kept them in line and out of the mainstream of the decision making process.
With the failure of the educational system, leadership and even such simple things as common manners has worked its way up the corporate and educational ladders. Leadership training is desperately needed at GM, but it has to be true leadership, not an academic construct.
HUMAN RESOURCES
American colleges turn out thousands of graduates with little or no education, and as a result there has been a negative effect on Human Resources. Employers try to paint a picture of their organization as a great place to work to try and land the few qualified applicants and those horribly underqualified applicants in training classes for a job they do not deserve.
Current HR directors, being a product of our educational system, have reduced HR to a system of canned policies and procedures constructed in an academic environment and, in most cases, out of touch with the real world. HR managers send out requests for extremely overqualified applicants, bypassing a large number of qualified job seekers and take the few provided by the staffing agency and ask them prepared questions and accepting or rejecting candidates based on answers constructed in the ivy halls. Scam artists already have the questions and give the “right” answers and naïve but qualified applicants are sent packing.
PAPERWORK LOG JAM
When there were no unions in the automobile industry, it was fashionable and profitable to buy up suppliers and fold their operations into yours. You not only could keep the profits but gained control over production and quality. With the advent of unions, pay scales started to march upward astronomically. Nowadays it is far more cost effective to outsource as much as possible to suppliers with lower wages.
Many companies had a long history of providing components to GM with acceptable cost, delivery and quality, but a lot of new plants sprang up with questionable abilities at much lower costs. So huge volumes of rules, constraints and oversight were developed to keep a tight rein on these suppliers and the old ones as well. With ISO and QS teaming up with Kaizen, Six Sigma, Lean Manufacturing and hosts of other constraints, suppliers are spending huge sums of money to complete paperwork which is dutifully stored at their expense and virtually never ever recovered, read or do anything but cost money and occupy space. Dump the unnecessary paperwork and eliminate the wasted efforts of useless employees. This will reduce your costs signficantly.
DESIGN
The outsourcing of production to Mexico and China is costing us dearly in terms of good manufacturing jobs in the United States. Even more ominous is the outsourcing of intellectual jobs to countries such as India. The message is that, intellectually and educationally, we cannot lend credible support to our industries that need top-drawer engineers to get the product to market.
Unfortunately, until we can train designers and engineers to turn out acceptable work, GM must begin outsourcing much of its work to people who can get the job done. Ultimately, the job must be brought in-house and GM must start a crash program to turn out qualified designers and then give them carte blanche to bring their creativity to the drawing board. Getting away from GM’s penchant of designing cars by committee will go a long way towards returning them to the number one spot again.
PERFORMANCE PAY
Giving workers bonuses based on profits seems like a good idea. In fact, that is how Executive salaries should be computed. But lazy and arrogant line workers quickly regard it as an entitlement without any additional performance required. Free money would devolve into another cost anchor around the neck of GM.
If you watch a GM assembly line in action, you will see the $73 per hour employees (including benefits) working at about one quarter the speed of the $6 dollar per hour MacDonald's employees at lunch time. Worse yet, you can view a bunch of people lurking around in the background doing nothing for the same pay. If you tie pay to cost and performance, employees will make certain that everyone is doing something useful. Tell some workers in a subassembly operation that they can go home when they are done with a day’s production and few will be around after four hours.
EDUCATION
When the military started drafting college students for the Vietnam War, colleges reacted by making the 2.0 grade a minimum for any class, therefore insuring a draft exemption for any full-time college student. The 3.0 became the average and schools learned that if they wanted to keep their students and a ton of tax money, they needed to inflate grades to a high level regardless of any academic achievement.
The result has been catastrophic. Courses were watered down, and broad based education eliminated. As the number empty diplomaheads increased and filtered into the job market, the ability to meet the needs of corporate America and the educational system was seriously compromised.
Forty years later, corporate America has no leaders; the schools are turning out barely literate graduates; and the “scholars” who have moved into the professorial ranks are perpetuating the educational bankruptcy of our schools. Many college professors are barely literate themselves and have made themselves busy creating canned programs like Six Sigma that allow graduates of their schools to appear functional in their jobs.
Therefore General Motors must invest and begin training their own students with courses specifically geared to meet the needs of the company.
SICK SIGMA
American coroporations looked at the Japanese threat coming and focused on Kanban and Kaizen as if these guidelines were their driving forces. No one seemed to understand that lean manufacturing is a way of life and not a corporate paperwork requirement.
As a response, Six Sigma, lean manufacturing and other such garbage was created at Universities by Professors and MBA students who have no concept of getting the job done. It is an escape hatch to let the legions of incompetents justify their existence by turning out reams of paperwork with words that scare people into thinking that their efforts are worthwhile. It’s time to dump the mountain of useless paperwork and worthless canned seminars that plague corporate America. It's time to address the real problems and come up with real solutions.
DEFERRED COMPENSATION
Good people are hard to find; and GM would be well advised to identify the top performers and tie their pay scales to some form of deferred compensation. It may start out small but over the years, an employee would be looking at losing a substantial monetary reward in deferred compensation by going somewhere else. If properly funded, the deferred compensation could be paid for entirely out of the interest generated by the fund. The last thing GM wants to do is to invest in training its employees only to let them take their skills over to Toyota.
SPINNING WHEELS
If GM could put as much spin on a flywheel as they do in their press releases, cars could run forever without gasoline. It's disheartening to listen to GM take every possible spin on every issue and try to make disaster look good.
Dump the faux PR releases and let the vehicles speak for themselves. Word of mouth sent millions of customers to the Japanese, and word of mouth is the best way to bring them back. No press release is going to do that. Building the best damn cars on the road will.
Offer a decent incentive to all "test drivers" of new vehicles, say a $500 factory rebate off the sticker price if they actually buy a GM product. I believe if you can first get them into a GM automobile, they will seriously consider buying it. The rebate is a bit of a come-on, but could actually sway someone who is considering another brand.
All GM cars should come with a 100,000 mile warranty, just like Hyundai. The image that sends to the public is "We got the best damn cars in the world and we're not afraid to back them up!"
TIER SUPPLIERS
Tier suppliers are sick of GM engineers, quality personnel and liason employees coming into their plants and throwing their weight around, requiring massive questionable changes, and running up huge expenses with no positive economic result. GM personnell should not approach tier suppliers arrogantly, but with an attitude of cooperation and help.
COST OF STEEL
The problem of steel shortages and the resulting high costs have been an unacceptable burden on GM and its tier suppliers. Investing in a full service steel manufacturer dedicated to strictly the supply of what the company needs is almost mandatory in order to provide a more stable price and supply protection.
THE DELPHI ORACLE
What do you do when one of your major component suppliers is on the verge of bankruptcy? Delphi would like "deep pockets" GM to come and rescue the failing enterprise. Excuse me, but "deep pockets" currently has a liquidity problem of its own. Ford chose to go the other route and repurchased Visteon in hopes of adding value to the company. GM, on the other hand, should immediately start outsourcing new backup suppliers from more cost effective arenas such as Korea and China. Let Delphi join the scrap heap of overburdened insolvent manufacturers. Then when it finally succumbs to defeat, scoop up the remains at bargain basement prices and rehire staff at half the present rates.

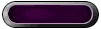